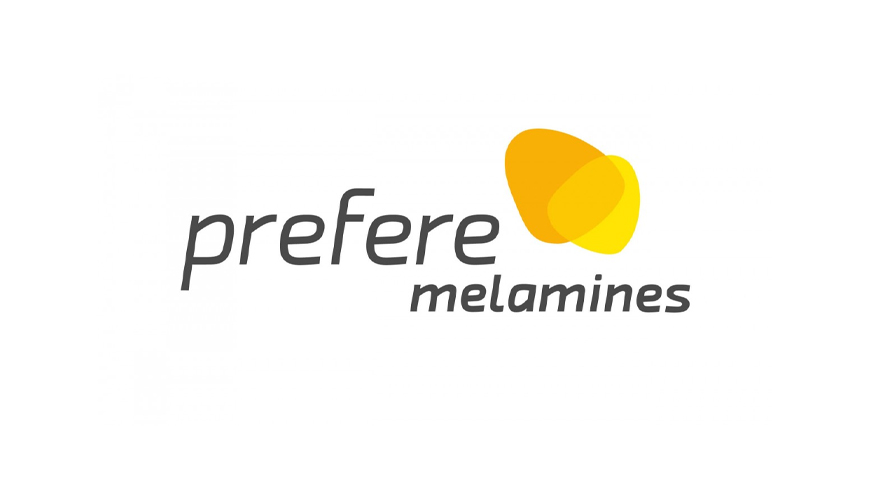
Growth Manufacturers Case Study
- Prefere Melamines
- Strategy
Prefere Melamines Continues to Improve Critical Customer Relationship
The Challenge
Prefere Melamines has days when everything goes great and days when they have issues. Their largest customer occasionally files a complaint, maybe once a year, because something is not right. In the past year Prefere Melamines had a contamination issue. One of the raw materials was contaminated and it affected their process significantly. They were unable to produce all of their products as scheduled. If the issue was not quickly resolved, they would begin to miss shipments to their customers.
A couple years ago, their largest customer suggested failure mode and effects analysis (FMEA) ase a beneficial tool for Prefere Melamines. FMEA is a step-by-step approach for identifying all possible failures in a design, process, or a product or service. The purpose of the FMEA is to take actions to eliminate or reduce failures, starting with the highest-priority ones. FMEA can change company culture from firefighting to a pro-active culture, and ideally it starts in the earliest conceptual design stages and continues throughout the life of the product.
Prefere Melamines had yet to find an FMEA training provider when their HR Manager discovered MassMEP, part of the MEP National Network™. They brought MassMEP in to deliver the training to all of their engineers and some of their managers. Prefere Melamines was able to use it as part of the investigation into the contaminant and, using the spreadsheet provided during the training, developed a more effective incoming raw material testing protocol. The FMEA process enabled the engineer that led the investigation to develop a number of action items and to implement process improvement.
The customer is pleased that Prefere Melamines had the training, as it provides another tool to improve their process and make sure they are better positioned to deliver the products the customer needs. Prefere Melamines has been audited by this customer many times over the 20 years that the operations director has been here. The customer has always been impressed with Prefere Melamines ability to lead in ways to prevent cratering and deliver high quality products on time. The lead auditor has told them, “You people get it – you know what we’re doing and what we’re trying to do. We wish all of our suppliers were at the level that you’re at.”
The Results
38 - 40
Retained Employees
Improved testing for raw materials will prevent this in future
Less time troubleshooting, more time on root cause by utilizing FMEA
FMEA training recognizes root cause, to avoid this in future
This gives us one more tool to help to improve our processes, to enable us to identify areas for improvement, and have a systematic approach to do that.
Scott Hansen
Operations Director
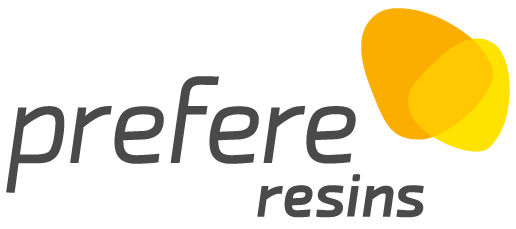
About Prefere Melamines
Prefere Melamines is a global supplier of amino cross-linkers for coatings and industrial applications. They provide high quality resins for high performance applications. Prefere Melamines is able to supply partners globally with production sites in Europe, the U.S. and Asia. Being so close to them also means that they operate efficiently and reliably. With 70+ years of experience, Prefere Melamines’ world-wide customers span several industries, including: automotive, coatings, construction, packaging, paint and ink, pulp and paper, rubber and tires, textiles, and decorative laminates.